Clean Room Monitoring Equipment
If you are looking for clean room monitoring equipment that helps you and your team eliminate manual logging, improve compliance readiness, and protect all your temperature-sensitive assets, you’ve arrived at the right place.
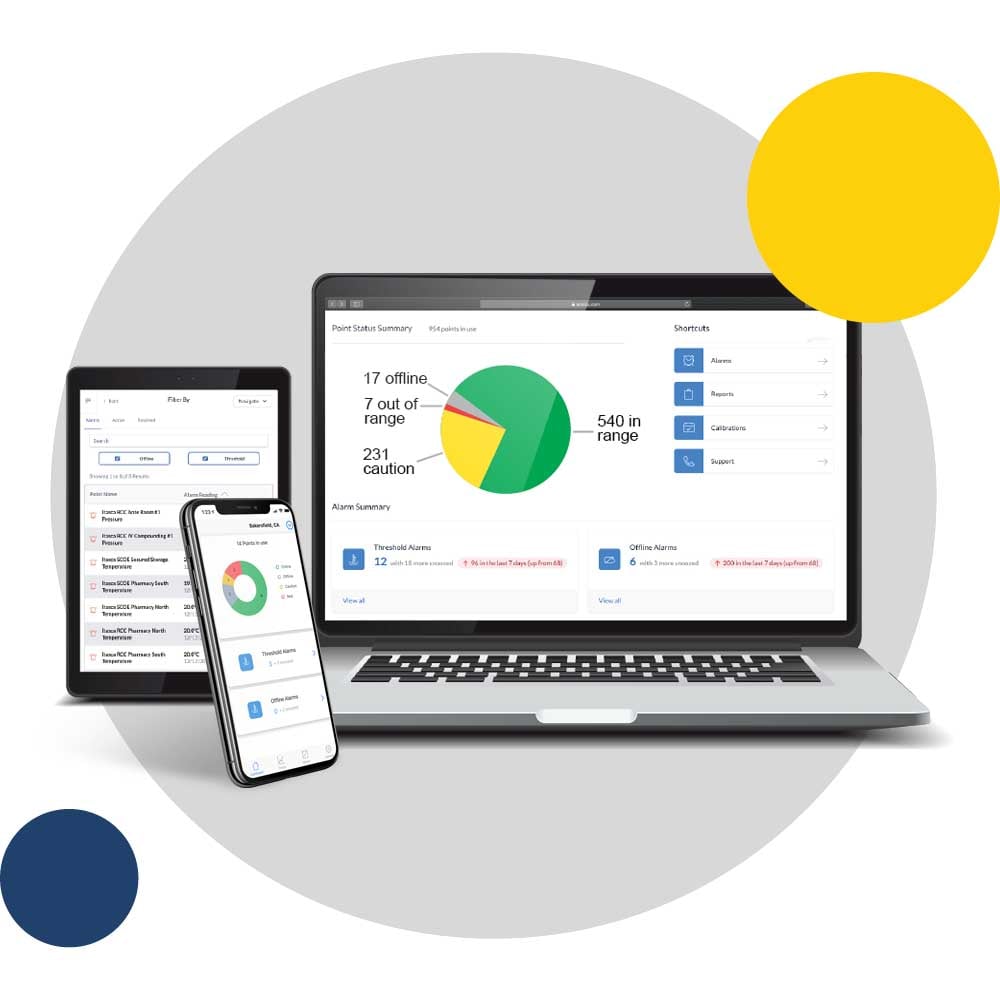
Let us help you evaluate your needs!
- Safety: Alerts via text, email, push notifications and phone calls to protect your precious assets
- Compliance: Automated compliance reports
- Efficiency: Reduced Manual Logging and time spent on reports
And what makes us different?
- Lifetime Warranty: Never buy hardware again!
- Unlimited Users: Scale across your entire organization
- Connectivity Flexibility: Wi-Fi, Cellular or Data Hub
- Phone call alarms: Alerts won't get ignored
- Mobile App: 500 Freezers in your pocket
- Facility monitoring: Simple to add water leak, door open, occupancy, and even IAQ monitoring
Engineered in Indiana with U.S.-based support.
See What Customers Say About Sonicu
Asset Protection. Compliance Automation. And Reduced Manual Processes.
Sonicu serves thousands of professionals at hundreds of organizations across North America by improving how they monitor and manage their most sensitive assets and environments.
Professionals from healthcare, life science, laboratory and cold chain facility management turn to Sonicu to help them improve the way they do business.
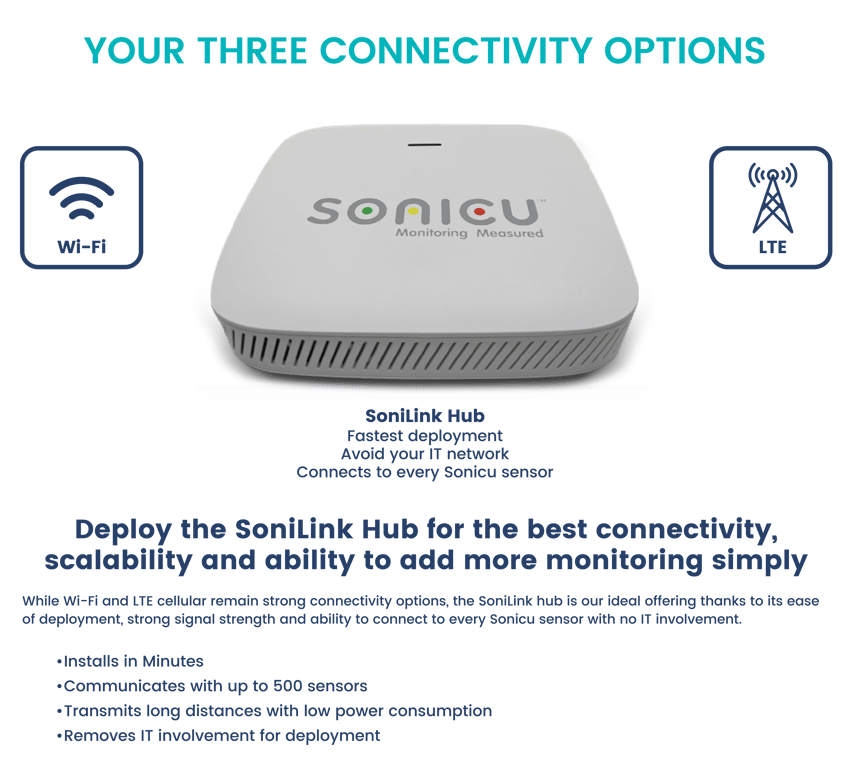
- Real-Time Monitoring: The sensors collect temperature data and transmit it wirelessly to Sonicloud - our cloud-based platform.
- Operational Efficiency: Virtually eliminate the need for tedious and costly manual logging
- Compliance Automation: Respond to virtually any regulatory audit or inspection in a few clicks with our reports section
- Asset Protection: Detect and respond to any temperature excursion that can threaten virtually anything perishable: food, drugs, vaccines, research, etc.
Our customers stay with us thanks to our American-based customer support, which is never more than a phone call away. While our technology is intuitive and powerful, we know it’s only as strong as the people who stand behind it.
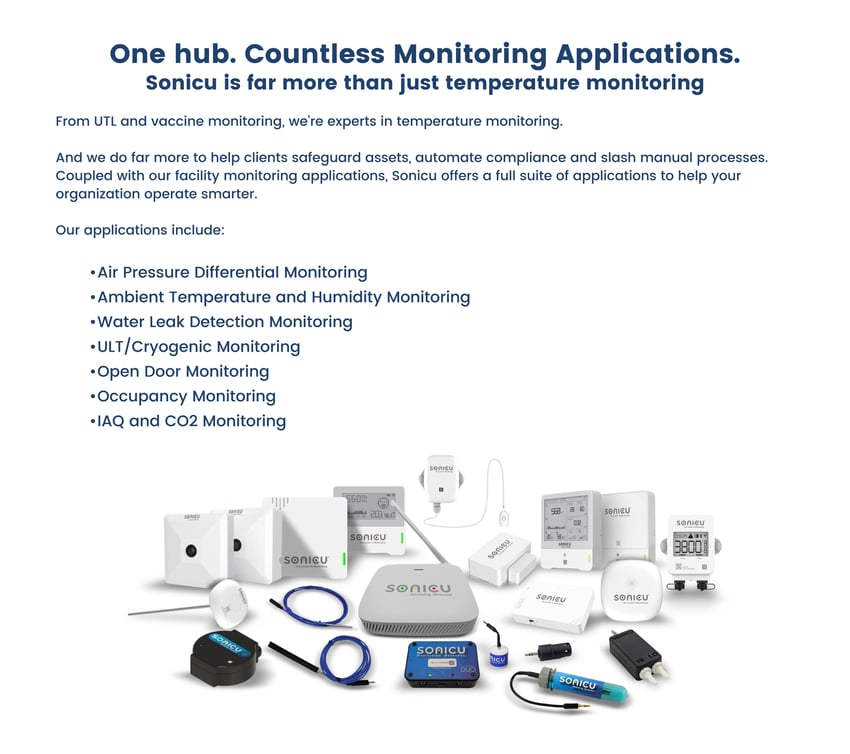
Cost competitiveness, great customer service, great control over the monitoring system, and low maintenance. You can't beat that.
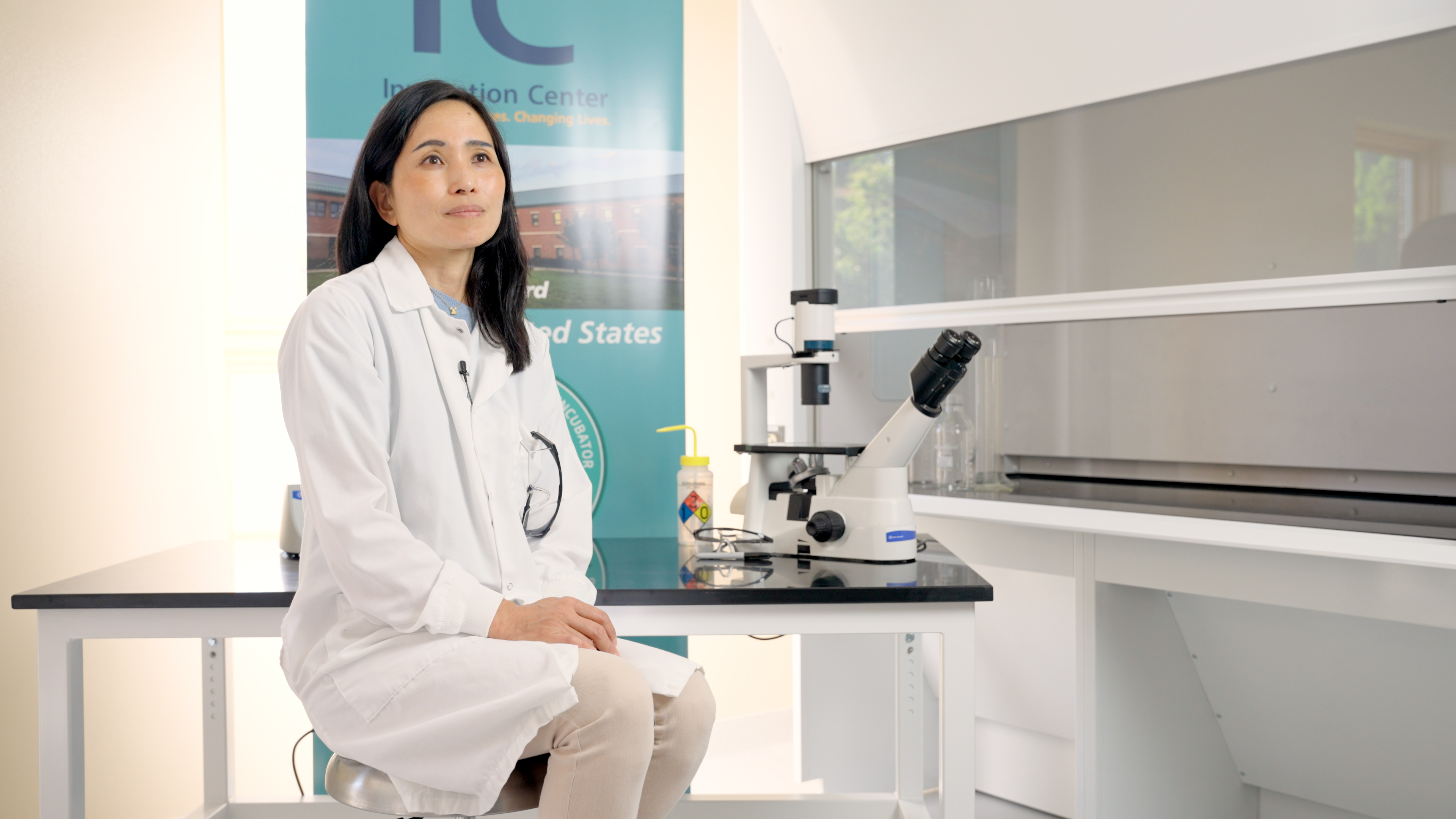
Sonicu costs are considerably more reasonable than our historic system, as well as other competitors on the market. The equipment is robust but simple to learn and utilize.
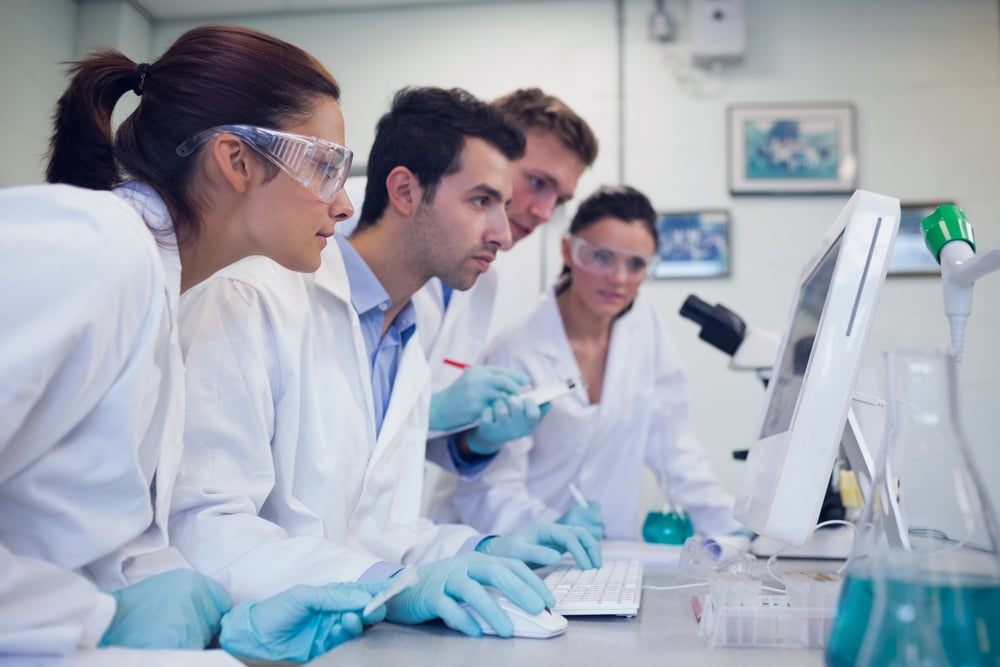
Having safe and secure storage provides reassurance that any future family building efforts will be protected. Sonicu gave us the ability to more easily put our head on the pillows and sleep easier at night knowing we had invested in a strong monitoring system.”
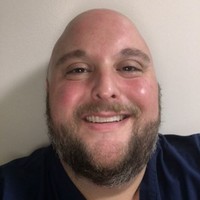
Navigating the Future of Precision: The Pivotal Role of Clean Room Monitoring Equipment
Clean room monitoring equipment plays a crucial role in maintaining the quality and standards of clean rooms across various industries.
Particle counters measure the concentration of particles in the air. They are essential for monitoring the cleanliness level of the clean room, as even tiny particles can significantly impact the processes carried out in such environments.
Environmental monitoring systems track various environmental parameters such as temperature, humidity, and air pressure. Maintaining these parameters at specific levels is crucial for the processes carried out in clean rooms.
Airflow monitors are used to ensure that the airflow patterns within the clean room meet the required standards. Proper airflow is essential for removing contaminants and maintaining a sterile environment.
In industries where sterility is critical (like pharmaceuticals or biotech), equipment for monitoring microbial contamination is essential.
In certain environments, the presence of specific chemicals or gasses must also be monitored and controlled.
Clean rooms in the pharmaceutical and biotechnology industries are used for the production of drugs and other biologically sensitive products, where contamination can have severe implications.
Semiconductor and electronics manufacturing industries require extremely low levels of particulates to avoid damaging the delicate electronics and microchips during manufacturing.
Also, in the manufacturing of spacecraft or defense equipment, even small particles can cause significant malfunctions.
Clean rooms are also used to manufacture devices that will be implanted in the human body, necessitating high sterility standards.
While not as stringent as pharmaceutical or semiconductor industries, certain high-risk food production areas utilize clean rooms to prevent contamination.
Many industries are governed by strict regulatory standards (like ISO or FDA regulations), and monitoring equipment helps ensure compliance.
Continuous monitoring also allows for the early detection of contaminants, preventing potential product spoilage or loss.
In some industries, such as chemical manufacturing, clean room monitoring equipment is also crucial for the safety of the personnel working in the clean rooms.
By ensuring that the clean room environment is consistently maintained at the required standards, these tools help avoid costly production errors and rework.
Clean room monitoring equipment is vital across various industries for maintaining the integrity of the clean room environment, ensuring product quality, compliance with regulations, and overall operational efficiency.
Founded in 2008 in Greenfield, Indiana, Sonicu began manufacturing noise monitors to protect vulnerable infants in neonatal intensive care units, and has evolved to monitor and protect a diverse set of sensitive conditions and environments including clean rooms.
What are the key components of clean room monitoring equipment?
The key components of clean room monitoring equipment are designed to ensure that the environment meets the stringent standards required for various sensitive processes. These components utilize advanced technologies to perform their functions effectively.
- Particle counters
- Detects and counts physical particles.
- A laser beam is passed through an air sample, and particles scatter the light, which is then detected and counted.
- Temperature sensors
- Use thermocouples, resistance temperature detectors (RTDs), or thermistors.
- Humidity sensors
- Utilize capacitive, resistive, or thermal conductivity measurement techniques.
- Pressure sensors
- Often based on piezoelectric or capacitive sensing technologies.
- Airflow monitors
- Anemometers (vane or hot-wire) or differential pressure sensors.
- Measure the speed and direction of airflow to ensure proper laminar flow and prevent stagnant air zones or cross-contamination.
- Microbial monitoring equipment
- Culture-based methods, particle counters with microbial detection capabilities, or ATP (adenosine triphosphate) bioluminescence.
- Identify and quantify microbial contaminants.
- Chemical sensors
- Electrochemical sensors, photoionization detectors, or gas chromatography.
- Detects and measures specific chemicals or gasses to prevent hazardous conditions or product contamination.
- Involves a variety of techniques, including electrochemical reactions and chromatography, to detect specific chemical compounds.
- Data logging and reporting systems
- Software systems integrated with sensors for data collection, analysis, and reporting.
- Record and manage data from various sensors, ensuring traceability and compliance with regulatory requirements.
- Optical sensing
- Used in particle counters and certain microbial monitors, where the interaction of light with particles or microbes is measured.
- Thermal sensing
- Employed in temperature and some humidity sensors, where changes in temperature affect the sensor's electrical resistance.
- Bioluminescence
- Used in certain microbial detection systems to measure ATP as an indicator of microbial presence.
- Data Analytics and IoT technologies
- For data logging and analysis, clean room monitoring systems often incorporate advanced data analytics and IoT (Internet of Things) capabilities, allowing for real-time monitoring and alerts.
By leveraging these technologies, clean room monitoring equipment can accurately and reliably measure and control the various parameters critical to maintaining the integrity of clean room environments. This technology ensures that the products manufactured or processes conducted within these clean rooms adhere to the necessary quality and safety standards.
Asset Protection. Compliance Automation. And Reduced Manual Processes. Sonicu serves thousands of professionals at hundreds of organizations across North America by improving how they monitor and manage their most sensitive assets and environments.
You can learn more about how our software helps compliance professionals in these case studies:
Problem: Pharmacy Suffered Too Much Humidity In New Wing, impacting Compounding Pharmacy
Solution: Affordable Humidity Monitoring that Delivered Powerful data to prompt contractors to fix improperly sized air handler
Problem: The dining department struck with regulatory violations
Solution: Enterprise-wide monitoring that automates regulatory compliance across all departments
Problem: Release of lead particles in battery projects
Solution: Mobile, affordable air pressure monitoring solution
What are the pain points that clean room monitoring equipment effectively addresses?
Clean room monitoring equipment addresses several critical pain points across various industries where maintaining a controlled environment is essential. These pain points are often related to quality control, regulatory compliance, and operational efficiency.
One of the primary challenges in clean rooms is preventing contamination, which can compromise product quality and safety, particularly in pharmaceuticals, semiconductors, and aerospace industries. Monitoring equipment continuously checks for particles, microbial contaminants, and chemical vapors, ensuring immediate action can be taken to mitigate contamination.
Industries like pharmaceuticals, biotechnology, and medical devices are subject to rigorous regulatory standards (e.g., FDA, ISO). Non-compliance can lead to legal issues and product recalls. Clean room monitoring systems ensure that environmental parameters are consistently within the required thresholds, aiding in regulatory compliance.
High standards of product quality are crucial, especially in industries where products have direct impacts on human health or safety. By maintaining an optimal clean room environment, clean room monitoring systems help ensure that the products manufactured meet the highest quality standards.
Unplanned downtime or product rework due to environmental issues can lead to significant financial losses. Real-time monitoring allows for quick adjustments to environmental conditions, reducing the likelihood of product defects and improving overall operational efficiency.
Keeping detailed records of environmental conditions is essential for quality control and audit purposes. Advanced data logging and reporting capabilities of monitoring systems provide comprehensive records for traceability and auditing.
Clean rooms are energy-intensive environments. Inefficient management of HVAC systems can lead to higher operating costs. Monitoring and controlling the environmental parameters can optimize the use of HVAC systems, leading to energy savings.
In some industries, such as chemical manufacturing, the presence of hazardous substances can pose safety risks to workers. Chemical sensors and environmental monitors help ensure worker safety by detecting harmful gasses and maintaining appropriate air quality.
As technology evolves, clean rooms must adapt to new standards and increased demands. Modern monitoring equipment is often scalable and adaptable, allowing for upgrades and integration with new technologies.
By addressing these pain points, clean room monitoring equipment plays a pivotal role in ensuring that industries can operate effectively while maintaining the highest standards of quality, safety, and efficiency.
Easy to install and configure and supported by live American-based phone support, Sonicu is the most affordable, intuitive, and trusted temperature and environmental monitoring solution nationwide.
You can learn more about how our software helps compliance professionals in these case studies:
Problem: Needed to reduce time to complete HACCP compliance reports
Solution: Self-install of temperature monitoring for compliance automation
Problem: Needed pharmacy temperature monitoring following refrigerator loss across many remote clinics:
Solution: Simple Sonicu installation and configuration simplified standing-up remote systems
Indiana University Health: Enterprise Hospital For Temp, Humidity, Air Pressure
Problem: Server Based Monitoring lacking Enterprise Visibility
Solution: One Window into all monitoring across dozens of facilities
Key benefits of clean room monitoring equipment
- Continuous monitoring ensures that the environment meets the necessary standards, which is crucial for maintaining product quality.
- These systems help in adhering to strict industry regulations (like FDA, ISO standards) by providing precise control and documentation of clean room conditions.
- Real-time monitoring allows for the immediate detection of particulate, chemical, or microbial contamination, preventing potential damage to products and processes.
- Especially in industries dealing with hazardous materials or processes, clean room monitoring equipment ensures a safe environment for workers by detecting harmful substances.
- Continuous logging of environmental data is vital for traceability, quality audits, and validation processes.
- By maintaining optimal conditions, these systems reduce the risk of product defects and rework, leading to more efficient operations.
- Smart monitoring can lead to more efficient use of HVAC systems, reducing energy consumption and operational costs.
Elevate Your Standards with Sonicu: Revolutionizing Clean Room Monitoring
In the intricate dance of maintaining the pristine conditions of clean rooms, the role of advanced monitoring equipment is not just significant—it's indispensable. As we've journeyed through the vital functionalities and the intricate balance of advantages and challenges associated with clean room monitoring, one fact remains crystal clear - the need for precise, reliable, and efficient monitoring solutions is paramount across a multitude of industries.
Sonicu stands at the forefront of this technology, offering a suite of monitoring solutions that are not just sophisticated, but also intuitive and adaptable to your specific needs. Whether it's pharmaceuticals, biotechnology, semiconductor manufacturing, or any industry where clean room integrity is non-negotiable, Sonicu's clean room monitoring equipment is engineered to ensure that your operations remain uncompromised, compliant, and efficient.
The investment in Sonicu's monitoring technology transcends the initial setup. It's an investment in peace of mind, knowing that your operations are safeguarded against contamination, your compliance with regulatory standards is streamlined, and your operational efficiency is optimized. Moreover, the long-term benefits of reduced waste, enhanced product quality, and operational reliability cannot be overstated.
However, we recognize that integrating new technology into your operations can seem daunting. That's why Sonicu is committed to providing not just equipment, but a partnership. Our team of experts is dedicated to guiding you through every step of the implementation process, ensuring that your transition to advanced clean room monitoring equipment is seamless and that your team is fully equipped to harness the full potential of our solutions.
Are you ready to elevate your clean room standards and embrace a future where quality, safety, and efficiency are not just goals, but guarantees? Let Sonicu be your guide in this journey. Contact us today to explore how our state-of-the-art clean room monitoring equipment can transform your operations. Together, let's set new standards of excellence in your industry.
American-based Customer Support: Robust & Reliable High Touch Service
Software and technology is only as good as the people who stand behind it.
At Sonicu, that means our team of American-based customer success managers who are never more than a phone call away to help field and fix any service issues.
Our probes and sensors are placed in demanding frozen environments and our software literally sends billions bits of data monthly, meaning there’s always the potential for a hiccup on either the hardware or software.
We are committed to fielding every customer service request promptly and addressing our customer’s concerns promptly and professionally.
“I like to say that every refrigerator or freezer is like a car in that they all behave a bit differently,
and then every now and then you just get a bad boy who doesn’t want to perform as we need it to,”
Martha Rardin, Director, Nutrition and Dietetics, Hendricks Regional Hospital.
“Sonicu has been a powerful tool to identify which units are behaving out of spec and get our team
to fix them before we have a serious issue.”
Tim Livesay, Director, Hancock Regional Hospital Pharmacy Director
Before Sonicu, we had to don bunny suits to check the status of our cleanrooms. Now we check our phones and know right away. The system saves us time and effort and helps us respond to environmental